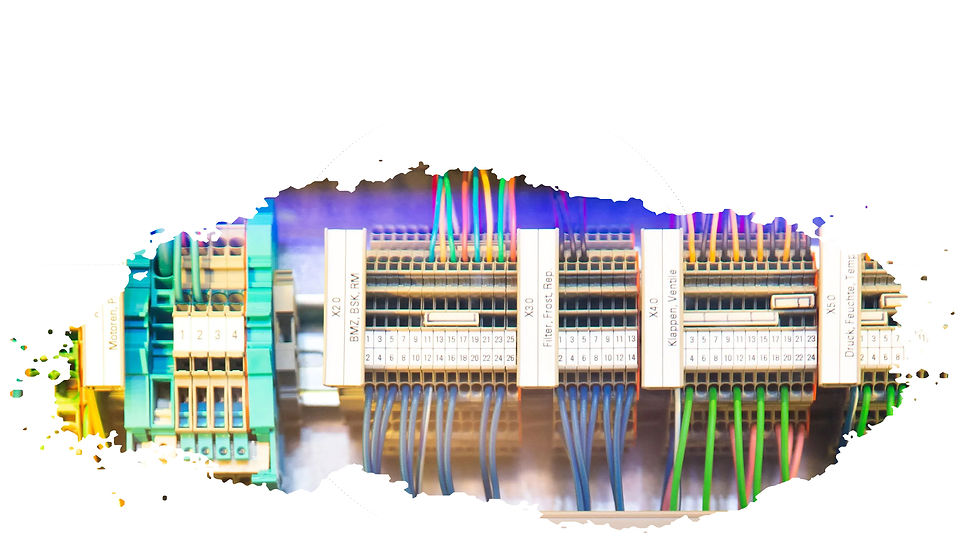
DCS
DCS (Distributed Control System) is a type of control system used for the automation and control of complex industrial processes. DCS systems are typically used in large-scale industrial plants, chemical facilities, power plants, petrochemical plants, and water treatment facilities.
What is DCS?
DCS (Distributed Control System) is a control system used to monitor, automate, and control industrial processes using a range of control elements and subsystems. DCS comprises distributed controllers and input/output (I/O) units along with one or more central control units.
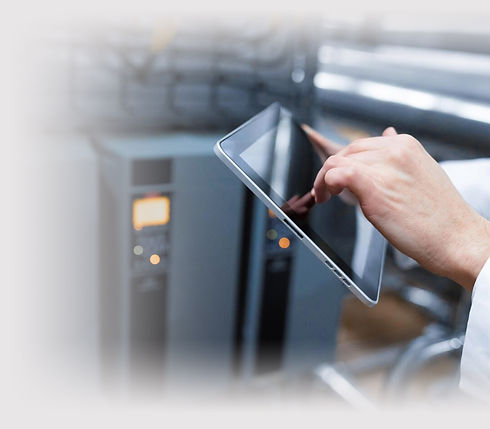
Main Features of DCS Systems
Distributed Architecture: DCS systems include multiple controllers and I/O units for process control. These controllers communicate via a network and work synchronously.
Central Monitoring and Control: DCS systems are used to monitor and control all processes of a facility through a central control room or operator station.
User-Friendly Interface: Operators use a user-friendly graphical interface to understand the facility's status and intervene when necessary.
Big Data Storage: DCS systems continuously record process data, allowing for analysis, reporting, and access to historical data.
Reliability: DCS systems include reliability measures such as redundant hardware and automatic error correction capabilities.
Basic Components of DCS Systems
Processor: The main processor of the DCS system processes signals from input and output devices, and sends signals to output devices.
Input Devices: Devices connected to the DCS system that sense the physical world around them, including switches, sensors, relays, limit switches, and others.
Output Devices: Devices controlled by signals from the DCS system, including motors, valves, lights, and others.
Network: The network connects various components of the DCS system, utilizing different protocols such as Ethernet, ControlNet, DeviceNet, and Profibus.
Software: Software ensures the operation of the DCS system, defining relationships between input and output devices and performing real-time control tasks.
Applications of DCS Systems
Chemical Industry: Control of chemical reactors, mixing processes, temperature, and pressure management.
Power Plants: Energy production, electricity distribution, and facility security.
Petrochemical Plants: Refinery operations, crude oil processing, storage, and distribution.
Water and Wastewater Treatment Plants: Liquid levels, chemical dosing, and water quality monitoring.
Advantages of DCS Systems
Monitoring and control of complex processes: The ability to effectively manage large and complex industrial processes.
High efficiency: Storage and analysis capabilities of big data for analyzing and optimizing process data.
Remote monitoring and control: The ability for facility operators to remotely access and monitor operations.
Redundant and reliable: Redundant hardware and automatic error correction enhance system reliability.
Food and beverage industry: DCS systems are used to control production processes in food and beverage facilities.
DCS systems play a significant role in increasing the efficiency of industrial facilities, reducing costs, and making operations safer. They enable the effective control of large and complex processes and provide operators with the ability to understand and analyze process data.
Disadvantages of DCS Systems
Cost: DCS systems may be more expensive compared to other automation systems.
Expertise: Using DCS systems may require expertise.
Differences between DCS Systems and PLC Systems
-
DCS systems are more complex and scalable.
-
DCS systems operate in real-time.
-
DCS systems typically use more advanced network protocols like Ethernet.
-
DCS systems often employ more sophisticated software.
-
DCS systems are more suitable for applications requiring complex and scalable control tasks, whereas PLC systems are more suitable for simpler, less scalable control tasks.